2025 Tác giả: Howard Calhoun | [email protected]. Sửa đổi lần cuối: 2025-01-24 13:27
Có một số lượng khá lớn các lỗi đường sắt khác nhau. Tất cả đều xảy ra vì những lý do khác nhau. Tổng cộng, có bốn loại thiếu hụt chính, do đó xảy ra sự cố. Công nghệ chế tạo và hàn kém theo dõi là nguyên nhân đầu tiên gây ra mài mòn. Nguyên nhân thứ hai là nội dung của đường dẫn quá thấp. Vật liệu có một tham số như độ bền mỏi do tiếp xúc, và nếu thông số này không đủ cao, thì đường ray cũng không sử dụng được. Lý do cuối cùng dẫn đến sự thất bại của các cơ sở này là do tác động của việc xe đầu kéo di chuyển qua chúng.
Nguyên nhân dẫn đến thất bại
Trong quá trình vận hành, các khuyết tật của đường sắt và khả năng xảy ra của chúng được tính toán dựa trên một số dữ kiện. Đầu tiên, một yếu tố quan trọng là lượng trọng tải đã chạy dọc theo đoạn tuyến. Thứ hai, tải trọng trên trục của đầu máy đóng một vai trò nào đó. Tốc độ của tàu hỏa cũng có thể ảnh hưởng đến tình trạng của đường ray. Thực hành và quan sát cho thấy rằngvào mùa ấm, tức là vào mùa xuân và mùa hè, số lượng vết đứt gãy giảm đi. Vào mùa thu, chỉ số này tăng nhẹ, mùa đông tăng gấp 2-3 lần so với mùa ấm. Có một lời giải thích cho điều này và nó nằm ở thực tế là ở nhiệt độ thấp, kim loại được đặc trưng bởi độ giòn tăng lên. Nói cách khác, sức mạnh tác động của nó bị giảm xuống mức tối thiểu. Tỷ lệ hỏng đường ray lớn nhất do lỗi đường sắt xảy ra vào tháng 3, nếu chúng ta nói về phần châu Âu của đất nước và cả vào tháng 4, nếu nó liên quan đến các khu vực phía đông và Siberi.
Máy phát hiện khuyết tật được sử dụng để phát hiện những vấn đề như vậy. 96,5% của tất cả các vấn đề đã xác định có thể được xác định bằng cách sử dụng các thiết bị di động hoặc di động. 2% khác được phát hiện bằng cách sử dụng thiết bị phát hiện lỗi ô tô và 1% khác sử dụng các mẫu khác của thiết bị này. Điều rất quan trọng cần lưu ý là có sự phân loại các khuyết tật đường sắt và mô tả chúng bằng cách sử dụng số. Điều này đã được thực hiện để có thể thực hiện tính toán tĩnh của đường ray.
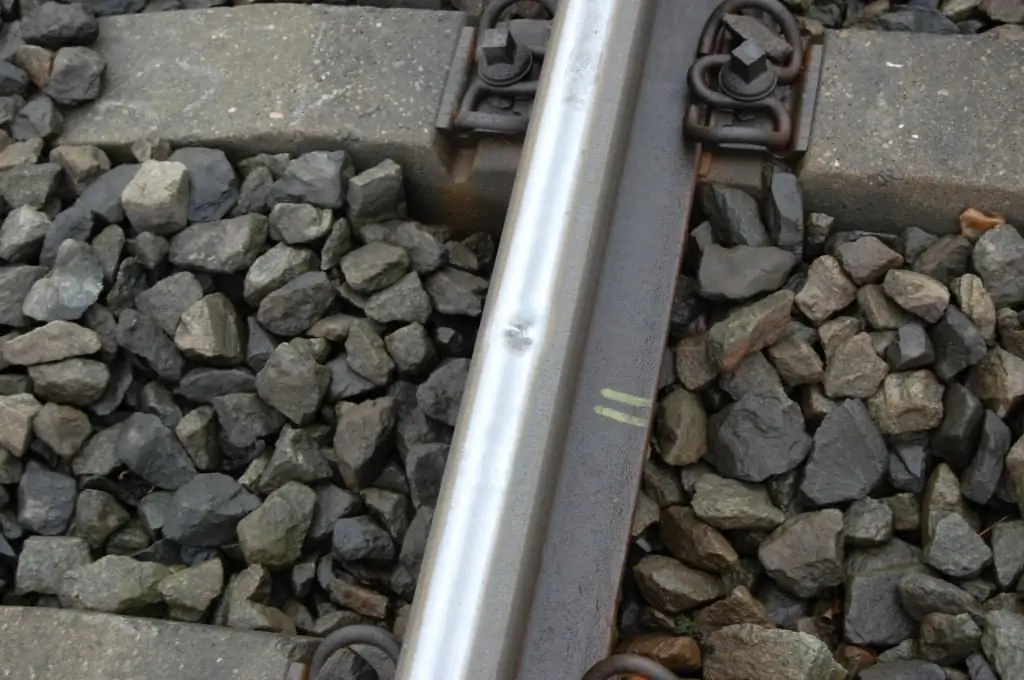
Phân loại
Mọi hư hỏng, đứt gãy hoặc khiếm khuyết trong các đoạn đường đua đều được chỉ ra bằng một hệ thống số thống nhất. Hai số đầu tiên là số chính, và số thứ ba là số phụ. Số đầu tiên cho biết loại khuyết tật hoặc hư hỏng của đường ray. Ngoài ra, nó còn cho biết vị trí xảy ra sự cố trên đoạn đường sắt. Chữ số thứ hai mô tả loại khuyết tật hoặc mô tả hư hỏng, có tính đến lý do gây ra lỗi đóđã xuất hiện. Chữ số phụ thứ ba cho biết vị trí của khuyết tật hoặc hư hỏng dọc theo chiều dài của đường ray. Chi tiết hơn, các khuyết tật đường sắt và phân loại của chúng được mô tả bằng các số từ 1 đến 9 cho ký tự đầu tiên.
- Nếu số đầu tiên là 1, điều đó có nghĩa là kim loại bị sứt mẻ và bong tróc trên bề mặt cán của đầu ray.
- Nếu số là 2, điều đó có nghĩa là các vết nứt ngang trên đầu ray đã được tìm thấy trên đoạn đường ray.
- Số 3 cũng cho biết sự hiện diện của các vết nứt trên đầu ray, nhưng thuộc loại dọc.
- Số 4 chỉ ra rằng các thay đổi về nhựa đã xảy ra, tức là bị dập, mòn dọc, nghiêng hoặc không đều.
- 5 là hư hỏng đường ray và các khuyết tật ảnh hưởng đến cổ.
- 6 là lỗi hoặc hư hỏng đế của thanh ray.
- 7 - đây là một biến dạng khá mạnh, vì hình này cho thấy sự xuất hiện của các đường gấp khúc dọc theo toàn bộ đoạn đường sắt.
- Nếu ngắt xảy ra trong mặt phẳng dọc và ngang, thì số 8 được gán thay vì số đầu tiên.
- Tất cả các khiếm khuyết, hư hỏng khác của đường sắt, v.v. không thuộc bất kỳ danh mục nào ở trên đều được biểu thị bằng số 9.
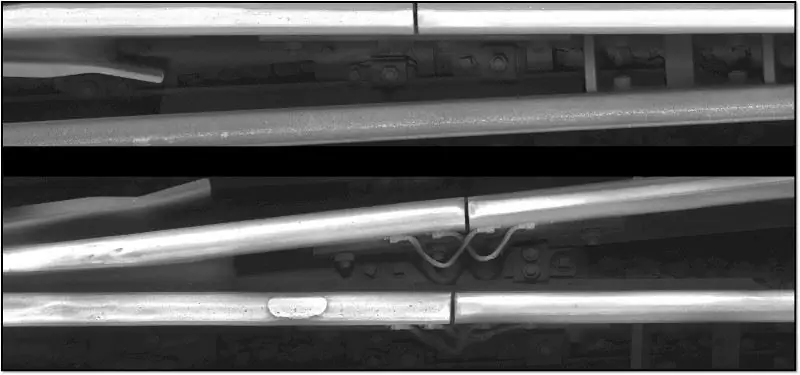
Xác định ý nghĩa của các số
Số thứ hai trong số chính của mã lỗi đường sắt cũng có nhiều giá trị, chính xác hơn là từ 0 đến 9.
- Nếu chữ số thứ hai là 0, điều đó có nghĩa là lỗi đã phát sinh do thực tế là đã có những sai lệch so với công nghệ khi tạo đoạn này của đường sắtsản xuất.
- Số 1 chỉ ra rằng chất lượng luyện kim của thép được sử dụng để sản xuất đường ray là không đủ. Cũng có thể độ bền của thép thấp hơn mức cần thiết cho hoạt động bình thường.
- 2 - chỉ ra rằng lỗi đã được thực hiện trong quá trình xử lý các phần cuối, do đó phần của đường dẫn bị lỗi. Ngoài ra, nó cũng bao gồm một số nhược điểm phát sinh khi xử lý các thanh ray.
- 3 - đây là những khiếm khuyết trong đường ray của đường ray, phát sinh do thực tế là các yêu cầu trong hướng dẫn bảo dưỡng hiện tại của đối tượng đã bị vi phạm. Nó cũng bao gồm thiệt hại do thực tế là các nguyên tắc của công nghệ xử lý lỗ bu lông trong lò luyện đã bị vi phạm.
- Nếu số thứ hai là 4, thì điều này có nghĩa là các vấn đề với đường ray đã phát sinh do tác động cụ thể lên chúng từ toa xe, chẳng hạn như do trượt. Điều này cũng bao gồm thiệt hại xảy ra do đầu máy không vượt qua kiểm tra thích hợp hoặc chế độ lái bị vi phạm.
- Số 5 bao gồm tất cả các hư hỏng do bất kỳ tác động cơ học nào từ bên ngoài, ví dụ như va đập vào dụng cụ, va vào thanh ray, v.v.
- Các lỗi hàn đường ray khá phổ biến là do hoạt động của máy hàn không đều. Chúng xảy ra trong các mối nối hàn và được đánh số 6.
- 7 - các vấn đề liên quan đến hoạt động của đường ray ở các khớp nối.
- 8 - đây là những sai sót phát sinh do bề mặt của đường ray, cũng nhưdo hàn khớp nối ray không đúng cách.
- Tất cả các vấn đề do ăn mòn gây ra đều được đánh số 9.
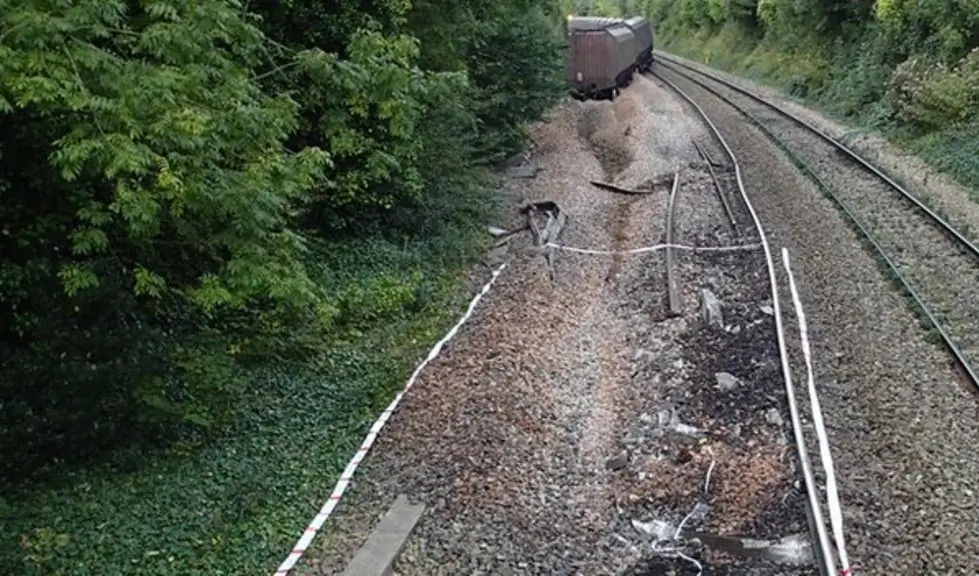
Điều cần lưu ý là sự cố một đoạn đường ray do đứt ray là hệ quả của việc tác động của nhiều nguyên nhân cùng một lúc. Thông thường, hóa ra là việc thiếu bảo trì đường sắt làm tăng nhanh sự phát triển của những sai sót được tạo ra trong quá trình lắp ráp hoặc hàn kết cấu. Do đó, việc xác định nguyên nhân trở nên khó khăn vì cần phải tìm ra chính xác nguồn chính gây ra sự cố. Các khiếm khuyết trong đường ray của đường ray xe lửa, hay nói đúng hơn là số của chúng cũng có chữ số thứ ba.
- 0 chỉ ra rằng sự cố đang hiện hữu dọc theo toàn bộ chiều dài của đường ray.
- 1 có nghĩa là vấn đề nằm ở chỗ chung, ở một số nơi. Có lẽ mối nối bắt vít bị hỏng, nằm cách cuối đường ray ít nhất 750 mm. Nếu chúng ta đang nói về một mối hàn, thì ở khoảng cách 200 mm đối xứng 100 mm trên mỗi phía của trục của mối hàn.
- 2 chỉ ra rằng các vấn đề nằm ở đâu đó bên ngoài khớp. Nếu chúng ta đang nói về kết nối bắt vít, thì bạn cần phải nhìn vào khoảng cách 440 mm đối xứng 220 mm ở mỗi bên của trục của mối hàn trong chân ray.
Các khiếm khuyết trong hàn đường sắt và các hư hỏng khác cũng được chia thành bốn loại, tùy thuộc vào mức độ phát triển của chúng. Có mức độ DP, D1, D2 và D3. Nguy hiểm nhất là DP. Chỉ định này chỉ ra rằng thiệt hại đã đạt đến các giá trị hoặc kích thước quan trọng. Những khu vực như vậy nênđược thay thế đầu tiên. Các khiếm khuyết được phân loại là D1 và D2 sẽ được sửa theo quy trình đã thiết lập, có tính đến cường độ của vấn đề. Các đường ray bị lỗi liên quan đến loại D3 chỉ được thay thế nếu người đứng đầu cự ly đường đua quyết định như vậy. Quyết định được đưa ra trên cơ sở dữ liệu do quản đốc truyền đi sau khi kiểm tra theo lịch trình và có tính đến mức độ phát triển của lỗi. Do đó, nó chỉ ra rằng mã lỗi đường sắt bao gồm ba chữ số, cũng như một dấu hiệu về mức độ phát triển của chúng trên đoạn.
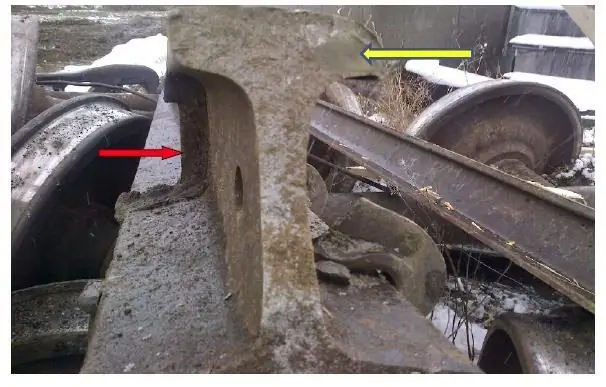
Phát hiện khuyết điểm
Phát hiện khuyết tật là một thủ tục để xác định các sai sót trong cấu trúc của đường sắt bằng cách sử dụng các thiết bị phát hiện khuyết tật đặc biệt. Điều đáng chú ý là các đường ray đi qua thủ tục này nhiều lần. Việc phát hiện khuyết tật đầu tiên được thực hiện tại nhà máy cán ray, khi cần đánh giá chất lượng của sản phẩm hoàn thiện. Quá trình xác minh tiếp theo diễn ra trong điều kiện hoạt động, tức là đang trên đường đi. Ngoài ra, quá trình xác minh được thực hiện trong các xưởng hàn đường sắt, nơi quá trình hàn không chỉ các kết cấu mới mà còn thực hiện sửa chữa hoặc hàn các kết cấu cũ.
Quy trình phát hiện lỗ hổng nhằm mục đích chủ yếu là xác định những khiếm khuyết đường sắt nguy hiểm nằm bên trong kết cấu, tức là chúng chưa có lỗ hổng ở bên ngoài. Điều này giúp bạn có thể thay thế cấu trúc bị hư hỏng một cách kịp thời.
Các loại vấn đề
Hiện tại, tất cả các loại khuyết tật, cách loại bỏ chúng, nguyên nhân dẫn đến sự xuất hiện của chúng,các phương tiện xác định của họ, v.v., được trình bày trong "Tài liệu quy định và kỹ thuật NTD / TsP 2002". Ngoài ra, đáng chú ý là còn có tài liệu thí nghiệm, cũng như phân loại các khuyết tật đường sắt NTD / TsP 1-93, theo đó tất cả các đoạn đường sắt có vấn đề được chia thành khuyết tật cấp tính (OD) và khuyết tật (D). Loại khuyết tật D với sự trợ giúp của NTD / CPU 2002 được chia thành một số lượng lớn các loại, tùy thuộc vào nguyên nhân xảy ra, mức độ phân bố và vị trí trên tuyến.
Đối với những đường ray có khuyết tật lớn là những mối đe dọa trực tiếp đến chuyển động của đoàn tàu, bởi vì ảnh hưởng của một sai sót, chúng có thể bị sập ngay dưới bánh xe của đoàn tàu hoặc làm cho toa xe rời khỏi theo dõi. Nếu phát hiện thấy đoạn như vậy thì phải lập tức đổi đoạn mới hoặc đoạn cũ cách kho kilômét. Nếu các khiếm khuyết mới trên đường ray được phát hiện trước khi thời hạn sử dụng của chúng hết hạn hoặc nếu trọng tải được đưa qua chúng ít hơn so với quy định trong tài liệu, thì khiếu nại đối với nhà máy luyện kim nơi chúng được sản xuất. Nếu lỗi được phát hiện tại mối hàn cũng trước thời hạn, thì khiếu nại sẽ được gửi đến nhà máy hàn đường sắt.
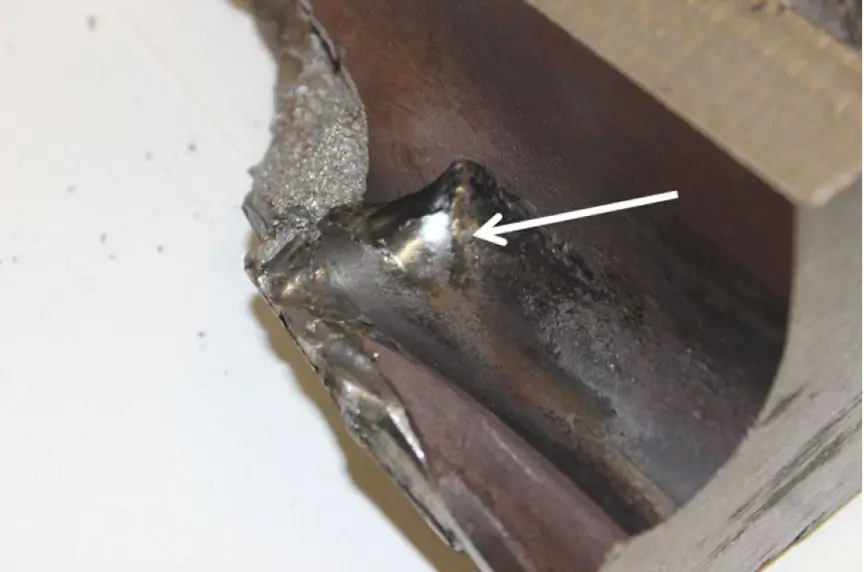
Đường ray bị lỗi bao gồm những đoạn đường ray, do tuổi thọ lâu dài, bắt đầu không sử dụng được. Dự kiến sẽ có sự hình thành các lỗ hổng trong các lĩnh vực như vậy. Tuy nhiên, họ vẫn phải đảm bảo cho toa xe qua lại an toàn. Mặc dù trongTrong một số trường hợp, giới hạn tốc độ được đưa ra khi đi qua một đoạn đường như vậy. Phiên bản mới của các lỗi đường ray và cách phân loại của chúng được trình bày chính xác trong tài liệu kỹ thuật và tiêu chuẩn NTD / CPU 2002. Các giá trị mã của các vấn đề có thể xảy ra đã được trình bày ở trên.
Tách thành các vùng khuyết và khiếm khuyết rõ rệt
Tài liệu cho biết tốc độ tàu được phép di chuyển dọc theo một đoạn cụ thể của đường ray. Nếu mức độ phát triển của khuyết tật thuộc nhóm DP thì tốc độ di chuyển không quá 40 km / h cho đến thời điểm loại bỏ. Hạng D1 cho phép tốc độ không quá 70 km / h, D2 - không quá 100 km / h. Flaws thuộc nhóm D3 không hạn chế tốc độ di chuyển của toa xe.
Ngoài ra, có một khung thời gian được thiết lập để thay thế từng nhóm đường ray bị lỗi. Nếu không có sự thay thế nào xảy ra trong khoảng thời gian đã thiết lập, danh mục sẽ được thay thế bằng danh mục cao hơn. Nói cách khác, DP3 đi đến D2, D2 đến D1, D1 đến DP. Đương nhiên, với mỗi lần chuyển đổi, thời hạn thay thế trở nên nghiêm ngặt hơn và giới hạn tốc độ cho chuyển động cũng tăng lên, phù hợp với các tiêu chuẩn đã thiết lập.
Các khiếm khuyết trong đường ray và cách phân loại mới của chúng theo NTD / CPU cũng xác định các vấn đề biến phần đường ray thành trạng thái đường ray bị lỗi nghiêm trọng hoặc đơn giản là lỗi. Để OD thuộc các vấn đề như:
- Xảy ra các vết nứt ngang, dọc hoặc ngang ở đầu ray. Thông thường, phân tích thuộc nhóm thứ hai và thứ ba, và mã của chúng là 20, 21, 24, 25.
- Nứt trong lỗ bu lông vớimã số 53, cũng như các vết nứt trên cổ ray, bất kể kích thước, cũng như các mã số 50, 55, 59 và 56.1.
- Xảy ra hiện tượng ăn mòn hoặc mòn cục bộ của ray có mã số 69, các vết nứt phát sinh do mỏi ăn mòn, nứt đế của ray có mã số 60, 64, 65, 66, cũng như các vết nứt ngang của ray.
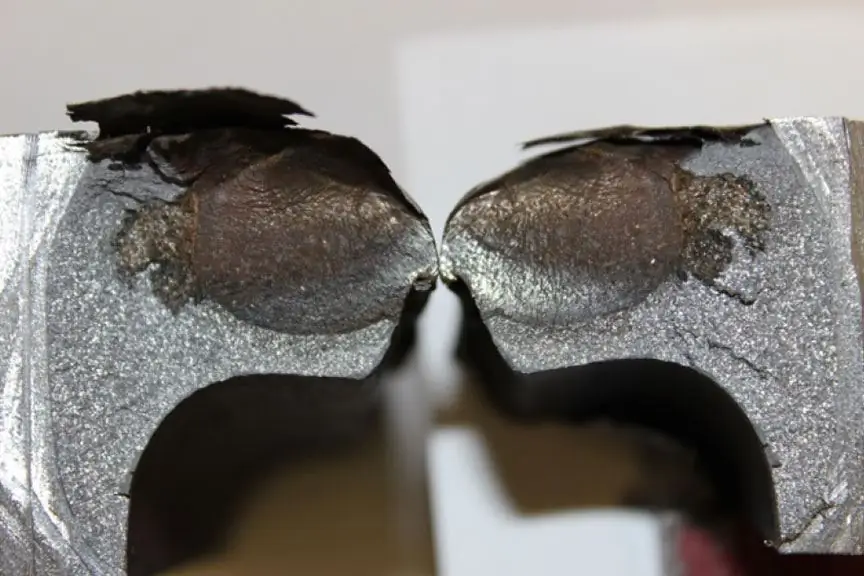
Sự xuất hiện của bất kỳ khiếm khuyết mới này dẫn đến thực tế là ngay cả một đoạn đường sắt mới cũng rơi vào trạng thái ML và phải được thay thế khẩn cấp. Có một số dấu hiệu nhận biết đường ray bị lỗi trong đường nhận và đường ray khởi hành. Chúng bao gồm:
- vượt quá mã giảm chuẩn hóa 41 + 44, mã bên 44, hoặc mòn đầu ray dọc;
- mẻ kim loại, nếu độ sâu không vượt quá 3 mm và chiều dài là 25 mm;
- sự hiện diện của trượt bánh xe đầu máy, mòn nhấp nhô.
Cũng cần nói thêm rằng tỷ lệ phần trăm lớn nhất của quá trình chuyển đổi đường ray bình thường sang loại bị lỗi xảy ra do vật liệu thiếu độ bền mỏi do tiếp xúc. Các vấn đề về khiếm khuyết như vậy trong đường ray và các bộ phận cử tri, cũng được lắp đặt trên đường ray, được phân loại theo mã 11 và 21. Nguyên nhân khá thường xuyên là do vấn đề 44, có nghĩa là đầu ray bị mài mòn nghiêm trọng. Khá thường xuyên có sự ăn mòn của đế của thanh ray - 69.
Đặc biệt là các khuyết tật nguy hiểm và nguyên nhân
Trước hết khi kiểm tra ray cần lưu ý những sự cố hư hỏng đó là do đâu."mỏi" của kim loại. Chúng được coi là nguy hiểm nhất. Chi tiết hơn, nó trông như thế này. Bánh xe lửa tiếp xúc với đường ray trên một diện tích khá nhỏ trong quá trình chuyển động. Chính qua khu vực nhỏ này, lượng điện áp khổng lồ mà một đoàn tàu đang chuyển động tạo ra sẽ được truyền đi. Chính những ứng suất tiếp xúc này, đặc biệt nếu chúng xảy ra ở vùng lân cận của đầu ray, sẽ khiến nó bị phoi hoặc dẫn đến bắn kim loại. Càng nhiều bánh xe đi qua khu vực này, kim loại càng "mỏi". Chính vì điều này mà các khuyết tật 11.1-2 được gây ra bởi một vấn đề như độ bền tiếp xúc của vật liệu thấp. Để tránh vấn đề này, hoặc ít nhất để làm cho đường ray chịu được nhiều chuyển động hơn, cần phải tăng cường độ bền của vật liệu thô.
Kim loại bị bong tróc hoặc bong tróc cũng có thể do sự hiện diện của các sợi tóc, mặt trời lặn hoặc bị giam cầm, có thể xuất hiện trên bề mặt của thanh ray trong quá trình lăn.
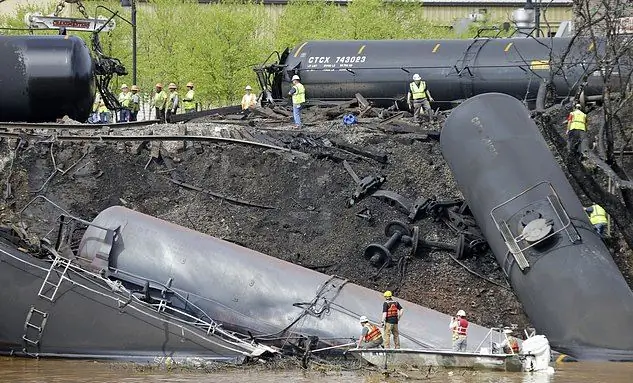
Các nhóm khuyết tật đường sắt như 20.1-2 và 21.1-2 được coi là rất nguy hiểm. Đối với nhóm khuyết tật thứ hai, chúng thường xuất hiện dưới dạng các vết nứt bên trong đầu hoặc các vết nứt bên ngoài xuất hiện ở khu vực đầu phi lê. Nếu sự cố như vậy xảy ra, thì đường ray sau đó có thể bị vỡ dưới sức nặng của một đoàn tàu đang chuyển động thành nhiều mảnh nhỏ. Đương nhiên, điều này sẽ dẫn đến tai nạn và rất có thể đoàn tàu sẽ chệch khỏi đường ray. Đối với các vấn đề với mã 20.1-2, chúngtự nảy sinh trong đầu, và lý do chính cho sự xuất hiện của chúng là những thiếu sót trong công nghệ sản xuất.
Lỗi đường sắt do kiểm tra kém
Điều đáng chú ý là vào ngày 23 tháng 10 năm 2014, việc phân loại lỗi đường sắt 2499 NTD / CPU đã được phê duyệt. Văn bản này có hiệu lực từ ngày 1 tháng 9 năm 2015 và bản thân tài liệu gồm 140 trang. Ngoài ra, một hướng dẫn mới về bảo trì các tuyến đường 2288 cũng đã được thông qua. Văn bản này có hiệu lực vào ngày 2017-01-01.
Những sai sót như 11.1-2 và 21.1-2 cũng khá thường xuyên do nhân viên quản lý đường bộ giám sát kém tình trạng của đường ray. Nếu trong thời gian đầu vận hành, mặt dưới ray không chính xác xảy ra thì ứng suất chính sẽ chuyển từ trọng tâm của mặt cắt sang mép nơi đặt đầu, tất nhiên sẽ dẫn đến mài mòn nhanh chóng. Tần suất xuất hiện các khuyết tật cũng tăng lên đáng kể nếu có sự vi phạm về độ nhẵn của các đường ray. Hơn nữa, điều quan trọng cần lưu ý là quá trình phát triển của sự xuất hiện của những vấn đề này có liên quan chặt chẽ không chỉ với việc bảo dưỡng đường ray không đúng cách, mà còn với những vi phạm trong việc chăm sóc phần lăn của chính đoàn tàu. Nếu sứt mẻ, thanh trượt và các sai sót khác xuất hiện trên bánh xe của ô tô, thì điều này sẽ ảnh hưởng lớn đến độ bền mỏi của kim loại và sự phát triển của nó.
Bên cạnh đầu, vấn đề thường xảy ra ở cổ ray - vết nứt ở khu vực lỗ bu lông, vấn đề chính. Thông thường, một vết nứt bắt nguồn từ đường viền của kết nối bắt vít, và sau đó để lại ở độ dốc 45 độ so với đường chân trời. Một phương tiện hiệu quả để chống lại những vết nứt như vậylà nội dung chất lượng của các khớp. Nói cách khác, cần phải siết các bu lông càng chặt càng tốt, để tránh hiện tượng đường ray bị võng hoặc lún. Vết nứt ở cổ giày cũng thường xuất hiện ở những vị trí đầu ray đi vào đế giày. Nguyên nhân chính dẫn đến sự xuất hiện của một khiếm khuyết như vậy là do một tấm lót đường ray được chọn không chính xác.
Về bản thân đế giày, ở đây thường không chỉ có vết nứt mà còn có vết thủng, đường viền. Tất cả điều này dẫn đến đứt gãy đường ray, xuất hiện các vết nứt dọc, và đẩy nhanh quá trình ăn mòn. Cách tốt nhất để đối phó với nhiều khuyết tật của đế là lắp một miếng đệm đàn hồi được đặt ngay dưới đế ray.
Vị trí của các khuyết tật và tên của chúng
Hiện tại, có những bảng khá lớn chỉ ra các lỗi chính của đường ray có thể xảy ra. Chúng cũng chỉ ra nơi xảy ra hư hỏng này hoặc hư hỏng đó, mã sự cố được chỉ ra chính xác. Những bảng như vậy trông như thế này.
Mô tả vấn đề | Vị trí hư hỏng trên ray | Mã khuyết |
Do vi phạm công nghệ sản xuất đường ray, có thể xảy ra sự cố như vết nứt hoặc sứt mẻ của kim loại trên bề mặt cán đầu | Vào và ngoài khớp | Tùy theo địa điểm, mã có thể là 10.1 hoặc 10.2 tương ứng |
Vết nứt hoặc sứt mẻ cũng có thể xảy ra ở một bên đầu hoặctrên phi lê. Chúng phát sinh từ bên trong dưới tác động của một số lượng lớn các tích tụ phi kim loại | Vào và ngoài khớp | Như trường hợp trước, mã có thể là 11.1 hoặc 11.2 tùy thuộc vào vị trí hư hỏng |
Có thể xảy ra sứt mẻ kim loại trên bề mặt gai. Nguyên nhân là do hiệu ứng động lực học trong các khớp của bu lông tăng lên | Ở ngã ba | mã thiệt hại này là 13.1 |
Có thể xảy ra hiện tượng bắn kim loại trên bề mặt gai của đầu ở khu vực mối hàn sau khi hết hạn bảo hành trọng tải | Khiếm khuyết mối hàn đường sắt | Flaw code 16.3 và 16.4 |
Vấn đề hư hỏng tương tự, nhưng trước khi trọng tải đảm bảo đã được vượt qua đường ray | Mối hàn | Khuyết điểm 17.3 và 17.4 |
Có thể xảy ra các vết nứt ngang trên đầu dưới tác động của các tác động cơ nhiệt do trượt hoặc trượt, ví dụ như | Xảy ra cả trong và ngoài đường may | 24.1 và 24.2 |
Do vi phạm công nghệ hàn hoặc vi phạm trong quá trình gia công mối hàn, các vết nứt ngang có thể xảy ra trên đầu. Điều quan trọng cần nói thêm là điều này có thể dẫn đến hỏng đường ray ngay sau khi thiếu trọng tải bảo hành | Mối hàn | 26.3 và 26.4 |
Nếu sự cố tương tự xảy ra như trường hợp trước, nhưng trước đó nó đã được bỏ quatrọng tải đảm bảo, sau đó vấn đề được chuyển sang hạng mục khác | Mối hàn vẫn như vị trí | Mã lỗi thay đổi thành 27.3 và 27.4 |
Nếu công nghệ sản xuất đường sắt bị vi phạm, các vết nứt dọc hoặc ngang có thể hình thành trên đầu đường ray. | Điều này xảy ra cả trong khớp và ngoài khớp | Mã hư 30.1 hoặc 30.2 |
Xác định khuyết tật đường sắt
Ngày nay, phương pháp duy nhất cho phép bạn phát hiện các khuyết tật mới trên đường ray ở giai đoạn đầu và ngăn chặn nó là phương pháp siêu âm.
Phương pháp kiểm tra không phá hủy này có thể phát hiện hư hỏng trong đường ray kim loại bằng cách sử dụng xung siêu âm. Phương pháp này được sử dụng trong nhiều ngành công nghiệp có gia công kim loại, nhưng phổ biến nhất là ở các ga đường sắt, nơi quan trọng nhất là giám sát chất lượng đường ray. Việc phát hiện khuyết tật bằng sóng siêu âm sẽ cho phép người lao động xác định nhanh chóng và chính xác các hư hỏng ẩn, đồng thời không ảnh hưởng hoặc phá hủy đối tượng nghiên cứu.
Phương pháp phát hiện khuyết tật đường sắt này có một số ưu điểm không thể phủ nhận.
Đầu tiên, và quan trọng nhất, là không có bất kỳ hư hỏng nào hoặc bất kỳ dấu vết nào khác để lại trên mẫu thử, tức là các khuyết tật mới. Thứ hai, giá thành của thiết bị này khá thấp và độ tin cậy của dữ liệu thu được do sử dụng nó là rất cao. Hơn nữa, điều quan trọng là đủmột thiết bị như vậy cho phép bạn tìm kiếm các khiếm khuyết đường ray mới vào bất kỳ thời điểm nào trong năm, điều này đặc biệt quan trọng.
Phương pháp siêu âm phát hiện khuyết tật cho phép bạn tìm thấy ngay cả những hư hỏng nhỏ nhất trong bất kỳ sản phẩm kim loại và mối nối nào. Vì lý do này, chúng cũng được sử dụng tích cực để kiểm tra lượt rẽ và các mối hàn kết cấu. Sử dụng thiết bị siêu âm, các hư hỏng sau có thể được xác định: sự xuất hiện của các vi phạm về tính đồng nhất của cấu trúc; kiểm tra những chỗ bị hư hỏng do ăn mòn; kiểm tra xem thành phần hóa học của thanh ray có tương ứng với thành phần được nêu trong tài liệu hay không.
Đề xuất:
Đường sắt Ukraina: tình trạng, đầu máy, cấu trúc doanh nghiệp. Bản đồ đường sắt của Ukraine
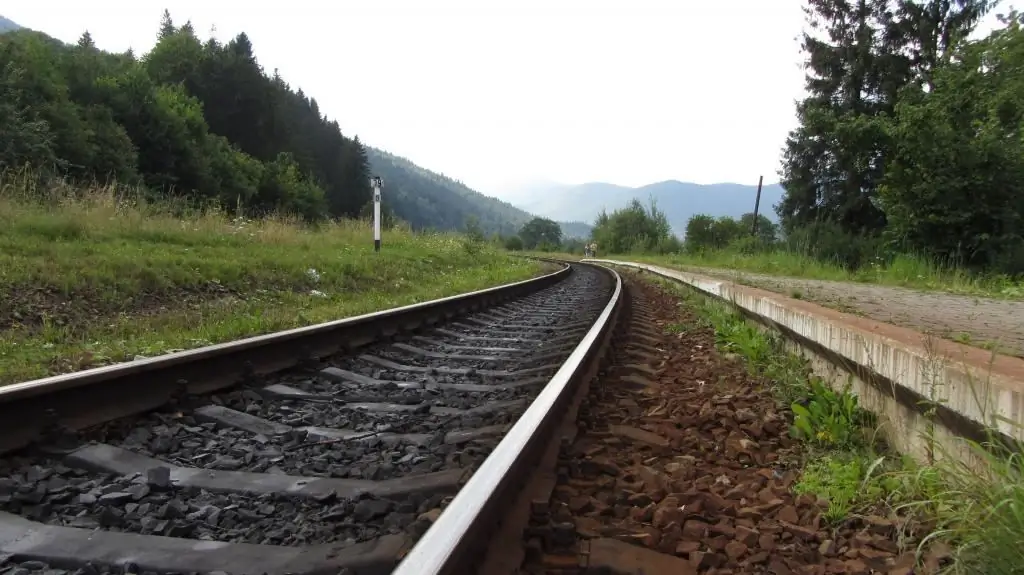
Ukraine đứng thứ 15 trên thế giới về độ dài của mạng lưới đường sắt. Tổng chiều dài của tất cả các tuyến đường sắt trong cả nước là 21.700 km. Một phần ba trong số chúng được nhiễm điện. Trong bài viết của chúng tôi, chúng tôi sẽ nói sơ qua về đường sắt Ukraine, đầu máy của chúng và tình trạng hiện tại
Căn hộ không phải nhà ở: định nghĩa pháp lý, các loại mặt bằng, mục đích của chúng, các văn bản quy định trong quá trình đăng ký và các đặc điểm của việc chuyển các căn hộ sang khô
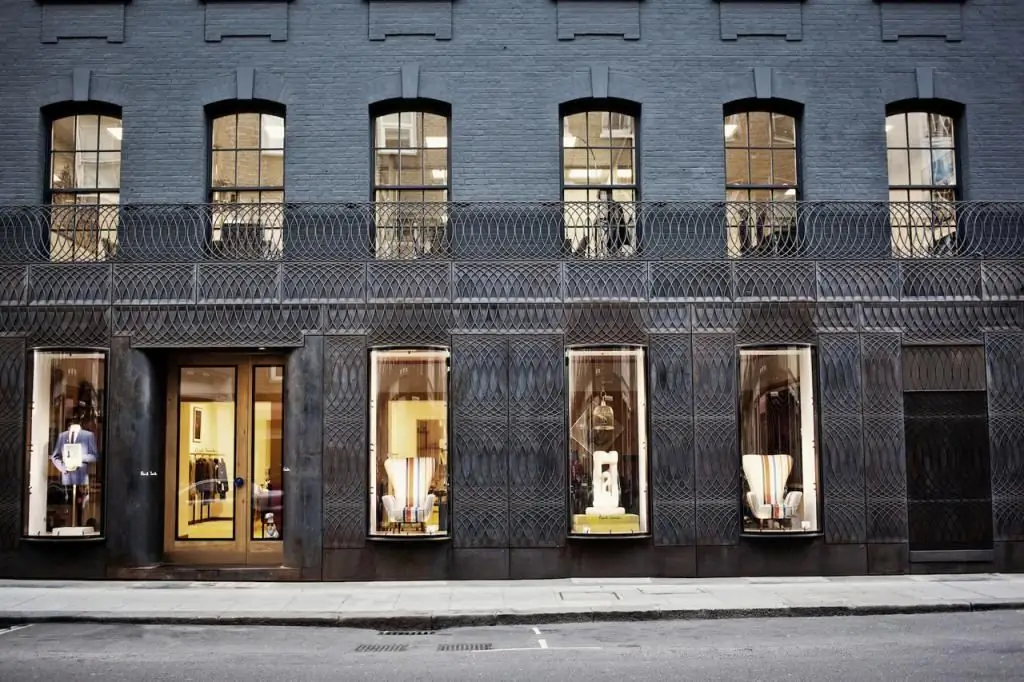
Bài báo xem xét định nghĩa của cơ sở không phải là nhà ở, các đặc điểm chính của nó. Lý do cho việc mua lại căn hộ ngày càng phổ biến với mục đích chuyển sang các cơ sở không phải nhà ở sau này được tiết lộ. Mô tả các tính năng của dịch thuật và các sắc thái có thể phát sinh trong trường hợp này được trình bày
Các loại và loại kế hoạch kinh doanh chính, phân loại, cấu trúc và ứng dụng của chúng trong thực tế
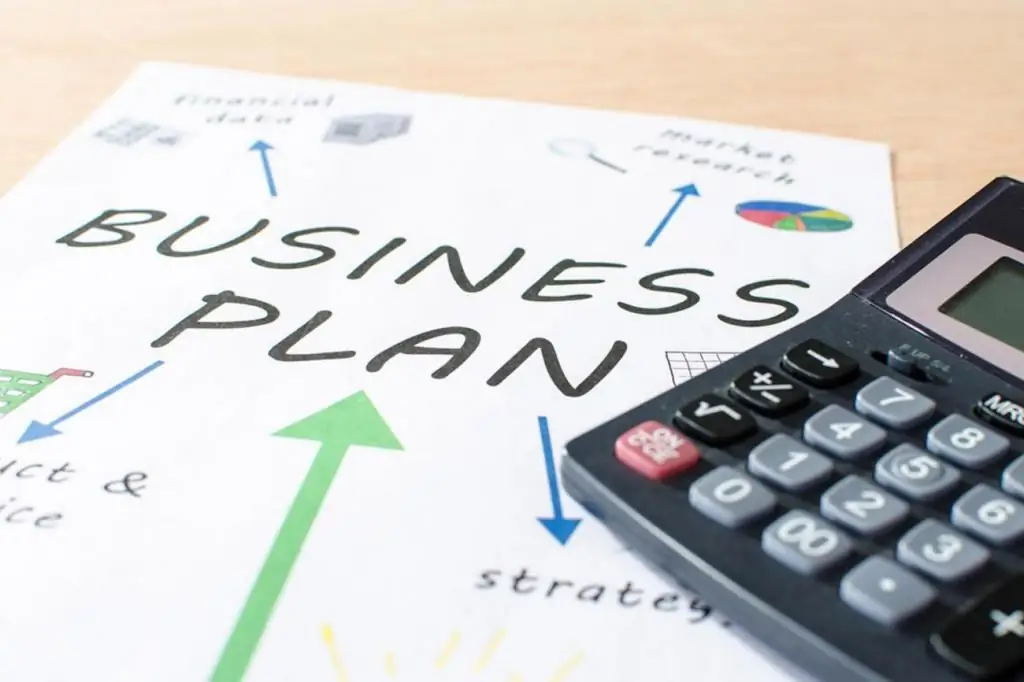
Mỗi kế hoạch kinh doanh là duy nhất, vì nó được phát triển cho những điều kiện cụ thể nhất định. Nhưng bạn cần tự làm quen với các tính năng của các loại kế hoạch kinh doanh để hiểu được các đặc điểm chính của chúng. Các chuyên gia khuyên bạn nên làm điều này trước khi biên soạn tài liệu tương tự của riêng bạn
Cơ cấu tổ chức của Đường sắt Nga. Đề án cơ cấu quản lý của Đường sắt Nga. Cấu trúc của Đường sắt Nga và các bộ phận của nó
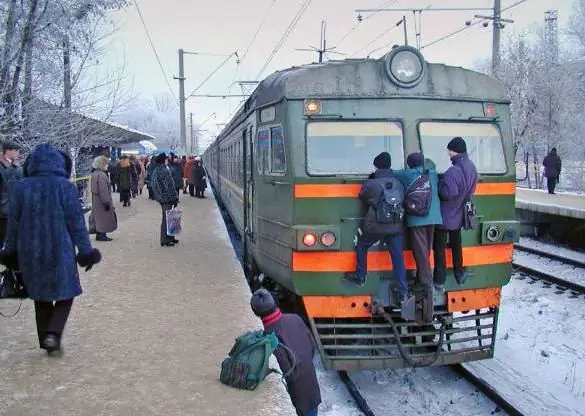
Cơ cấu của Đường sắt Nga, ngoài bộ máy quản lý, bao gồm các bộ phận phụ thuộc khác nhau, các văn phòng đại diện ở các quốc gia khác, cũng như các chi nhánh và công ty con. Trụ sở chính của công ty được đặt tại: Moscow, st. New Basmannaya d 2
Đường ray là Định nghĩa, khái niệm, đặc điểm và kích thước. Kích thước tàu và các tính năng của hoạt động cơ sở đường ray
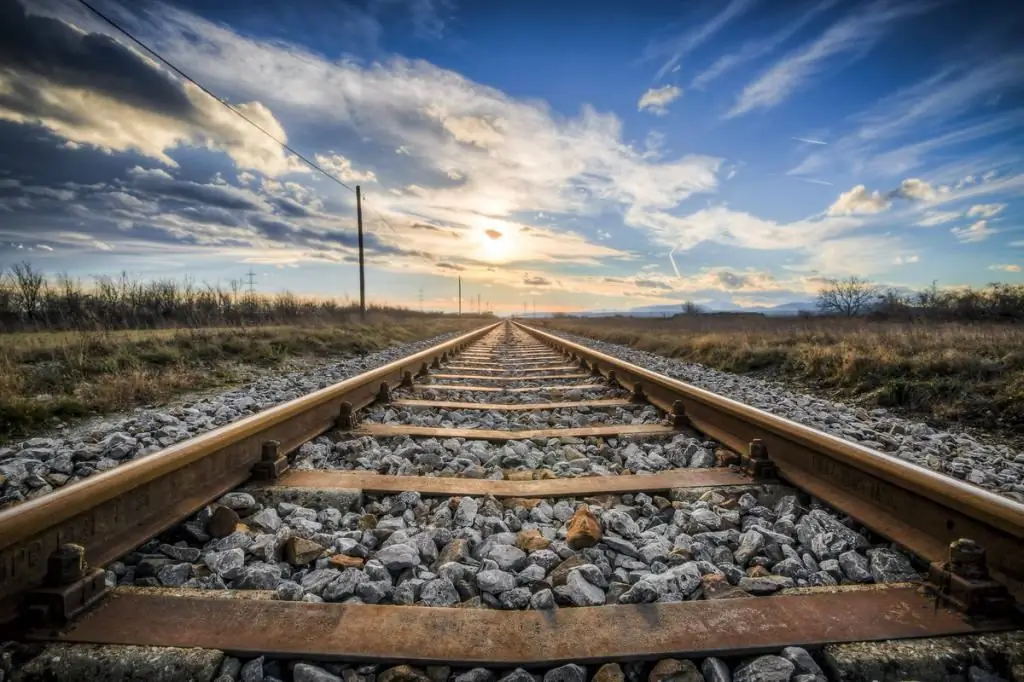
Đi tàu qua các thành phố và thị trấn, bạn có thể tìm hiểu rất nhiều điều thú vị và thú vị về thế giới của đường sắt. Đã hơn một lần, những người đi du lịch đã tự đặt câu hỏi về việc cái này hay đường ray kia dẫn đến đâu? Và người kỹ sư quản lý đoàn tàu có cảm giác gì khi đoàn tàu vừa xuất phát hoặc đến ga? Xe ô tô kim loại chuyển động như thế nào và đi từ đâu và đường đi của đầu máy như thế nào?