2025 Tác giả: Howard Calhoun | [email protected]. Sửa đổi lần cuối: 2025-01-24 13:28
Người đứng đầu bất kỳ doanh nghiệp nào, bất kể lĩnh vực hoạt động nào, đều mơ ước lợi nhuận tăng trưởng và chi phí sản xuất không đổi. Hệ thống "5S" trong sản xuất (phiên bản tiếng Anh là 5S), chỉ dựa trên việc sử dụng hợp lý nguồn dự trữ nội bộ, giúp đạt được kết quả này.
Hệ thống này không được tạo ra từ đầu. Một cái gì đó tương tự vào cuối thế kỷ 19 đã được đề xuất bởi Frederick Taylor người Mỹ. Ở Nga, điều này đã được thực hiện bởi nhà khoa học, nhà cách mạng, nhà triết học và nhà tư tưởng A. A. Bogdanov, người đã xuất bản một cuốn sách về các nguyên tắc quản lý khoa học vào năm 1911. Trên cơ sở các điều khoản đã nêu trong đó, Liên Xô đã đưa ra phương thức KHÔNG, tức là tổ chức lao động một cách khoa học. Nhưng hoàn hảo nhất là hệ thống 5C do kỹ sư người Nhật Taiichi Ohno đề xuất và được ông đưa vào sản xuất tại nhà máy Toyota Motor. Nó là gì và tại sao hệ thống tiếng Nhật lại trở nên phổ biến như vậy?
Thực tế là nó dựa trên nguyên tắc đơn giản là không đòi hỏi chi phí. Nó bao gồm trongtiếp theo - mỗi nhân viên, từ người dọn dẹp đến giám đốc, nên tối ưu hóa phần việc của mình trong quy trình làm việc tổng thể càng nhiều càng tốt. Điều này dẫn đến sự gia tăng lợi nhuận của toàn bộ hoạt động sản xuất và tăng thu nhập của tất cả nhân viên của công ty. Giờ đây, việc giới thiệu hệ thống "5C" đã được các doanh nghiệp trên toàn thế giới, bao gồm cả Nga, đón nhận. Trong bài viết này, chúng tôi sẽ cố gắng thuyết phục những người hoài nghi rằng bí quyết của Nhật Bản thực sự hiệu quả và hoàn toàn có hiệu quả trong bất kỳ lĩnh vực hoạt động nào.
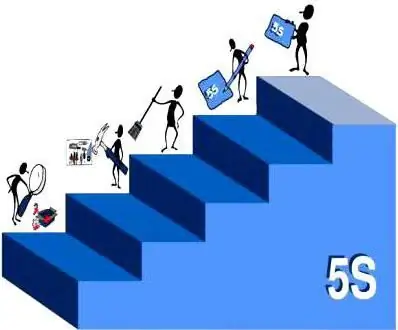
Hệ thống "5C" trong sản xuất, nó là gì
5S quốc tế là viết tắt của năm bước ("bước" trong tiếng Anh là bước). Một số nhà kinh tế học và những người ủng hộ thái độ làm việc mới giải thích tên gọi của năm định đề Nhật Bản được thực hiện nhất quán trong hệ thống 5S: seiri, seiton, seiso, seiketsu và shitsuke. Đối với chúng tôi, "5C" bản địa của chúng tôi gần gũi hơn và dễ hiểu hơn - năm bước liên tiếp cần được hoàn thành để đạt được sự thịnh vượng cho hoạt động sản xuất của chúng tôi. Đây là:
1. Sắp xếp.
2. Giữ trật tự.
3. Giữ sạch sẽ.
4. Tiêu chuẩn hóa.
5. Cải tiến.
Như bạn thấy, hệ thống "5C" không yêu cầu bất cứ điều gì siêu nhiên trong quá trình sản xuất. Có lẽ đó là lý do tại sao người ta vẫn có thể gặp sự ngờ vực và thái độ phù phiếm đối với cô ấy.
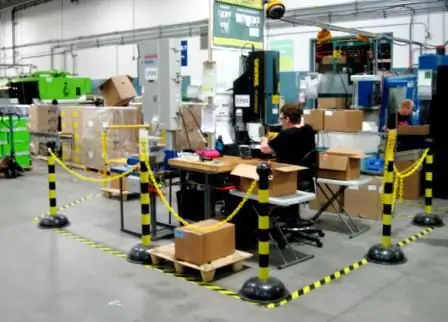
Các giai đoạn tạo hệ thống
Taiichi Ohno người Nhật thông thái, người nhờ giới thiệu các phương pháp của mình tại nhà máy Toyota, đã vươn lên từkỹ sư cho Giám đốc điều hành, nhận thấy có bao nhiêu tổn thất xảy ra do các mâu thuẫn và lớp phủ khác nhau. Ví dụ, một số ốc vít nhỏ đã không được đưa lên băng tải kịp thời, và kết quả là toàn bộ quá trình sản xuất đã dừng lại. Hoặc ngược lại, các bộ phận đã được cung cấp với một khoản tiền chênh lệch, chúng lại trở nên thừa và kết quả là một trong những nhân viên phải mang chúng về kho, đồng nghĩa với việc lãng phí thời gian của họ vào công việc trống rỗng. Taiichi Ohno đã phát triển một khái niệm mà ông gọi là "đúng lúc". Có nghĩa là, chính xác là nhiều bộ phận cần thiết hiện đã được chuyển đến băng tải.
Có thể đưa ra các ví dụ khác. Hệ thống "5S" trong quá trình sản xuất cũng bao gồm khái niệm "kanban", trong tiếng Nhật có nghĩa là "bảng hiệu quảng cáo". Taiichi Ohno đề nghị gắn cái gọi là thẻ "kanban" cho từng bộ phận hoặc từng công cụ, trong đó đưa ra tất cả thông tin cần thiết về bộ phận hoặc công cụ. Về cơ bản, nó áp dụng cho bất cứ thứ gì. Ví dụ như hàng hóa, thuốc men, thư mục trong văn phòng. Khái niệm thứ ba dựa trên hệ thống 5S trong sản xuất là khái niệm "kaizen", có nghĩa là cải tiến liên tục. Các khái niệm khác cũng được hình thành, chỉ phù hợp với các quy trình sản xuất chuyên môn hóa cao. Trong bài viết này, chúng tôi sẽ không xem xét chúng. Kết quả của tất cả các cải tiến được thử nghiệm trong thực tế, 5 bước đã được hình thành có thể áp dụng cho bất kỳ sản xuất nào. Hãy phân tích chúng một cách chi tiết.
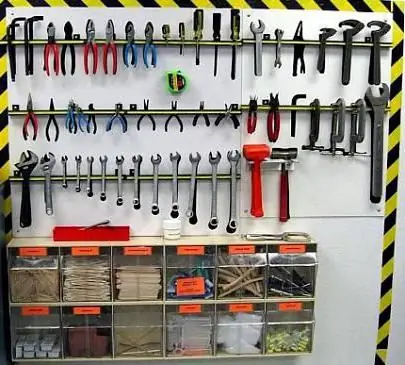
Sắp xếp
Nhiều người trong chúng ta có các vật phẩm trên máy tính để bàn của mình, trongvề cơ bản là không cần thiết. Ví dụ, biểu mẫu cũ, tệp không sử dụng, bản nháp các phép tính, khăn ăn trên đó có một tách cà phê. Và giữa sự hỗn loạn này có thể có những hồ sơ hoặc tài liệu cần thiết. Các nguyên tắc cơ bản của hệ thống "5S" liên quan đến việc tối ưu hóa quy trình làm việc của bạn, nghĩa là, đảm bảo rằng thời gian không bị lãng phí khi tìm kiếm những thứ phù hợp trong đống đổ nát của những thứ không cần thiết. Đây là phân loại. Có nghĩa là, tại nơi làm việc (gần máy móc, trên bàn, trong xưởng - bất cứ nơi nào), tất cả các vật dụng được bày thành hai đống - những thứ cần thiết và không cần thiết thì phải vứt bỏ. Hơn nữa, mọi thứ bạn cần được phân hủy thành các đống sau: “thường xuyên sử dụng và liên tục”, “hiếm khi sử dụng”, “hầu như không sử dụng”. Điều này hoàn tất việc sắp xếp.
Giữ trật tự
Nếu bạn chỉ tháo rời các mục, sẽ không có ý nghĩa. Cần phải sắp xếp các vật dụng (dụng cụ, tài liệu) này theo thứ tự sao cho những gì được sử dụng liên tục và thường xuyên ở trong tầm mắt, hoặc để có thể nhanh chóng lấy ra và dễ dàng cất lại. Những gì ít sử dụng có thể được gửi vào một nơi nào đó trong hộp, nhưng phải gắn thẻ kanban vào đó để sau một thời gian có thể tìm thấy dễ dàng và chính xác. Như bạn có thể thấy, hệ thống 5S tại nơi làm việc bắt đầu với những bước đơn giản nhất, nhưng trên thực tế nó lại mang lại hiệu quả rất cao. Và bên cạnh đó, nó giúp cải thiện tâm trạng và mong muốn làm việc.
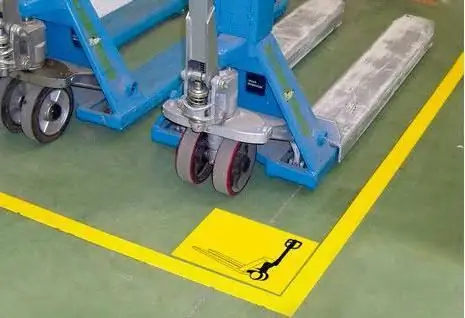
Giữ sạch
Bước thứ ba này là hợp lý nhất đối với nhiều người. Chúng tôi được dạy phải sạch sẽ từ thời thơ ấu. Trêntrong sản xuất cũng rất cần thiết, không chỉ bàn của nhân viên văn phòng hay tủ trong các cơ sở kinh doanh dịch vụ ăn uống mà máy móc, phòng tiện ích của người vệ sinh cũng cần phải sạch sẽ. Ở Nhật Bản, nhân viên chăm sóc nơi làm việc của họ rất tốt, họ được dọn dẹp ba lần một ngày - vào buổi sáng trước khi làm việc, vào giờ ăn trưa và buổi tối, khi kết thúc ngày làm việc. Ngoài ra, các doanh nghiệp của họ đã giới thiệu các khu vực đánh dấu đặc biệt cho phép họ quan sát trật tự trong sản xuất, đó là khu vực chứa thành phẩm, kho chứa một số bộ phận, v.v. được đánh dấu bằng các màu sắc khác nhau.
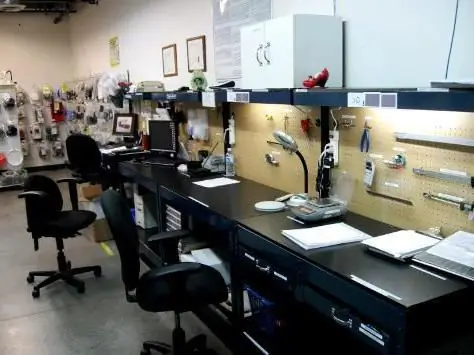
Chuẩn hóa
Các nguyên tắc tiêu chuẩn hóa được phát minh bởi Taiichi Ohno. Chúng cũng được sử dụng rộng rãi bởi hệ thống 5S hiện đại. Quản lý sản xuất, nhờ tiêu chuẩn hóa, nhận được một công cụ tuyệt vời để kiểm soát tất cả các quy trình. Nhờ đó, các nguyên nhân chậm trễ tiến độ nhanh chóng được loại bỏ và khắc phục những sai sót dẫn đến việc phát hành sản phẩm kém chất lượng. Tại nhà máy Toyota Motor, việc tiêu chuẩn hóa trông như thế này: các quản đốc lập kế hoạch làm việc hàng ngày, các hướng dẫn chính xác được dán tại nơi làm việc và vào cuối ngày làm việc, các công nhân đặc biệt kiểm tra xem những sai lệch nào so với kế hoạch xảy ra trong ngày và tại sao. Đây là quy tắc cơ bản của tiêu chuẩn hóa, đó là các hướng dẫn chính xác, kế hoạch làm việc và kiểm soát việc thực hiện chúng. Hiện nay, nhiều doanh nghiệp, ví dụ, các nhà máy ENSTO ở Estonia, đang giới thiệu một hệ thống tiền thưởng cho những nhân viên tuân thủ nghiêm ngặt các quy định của hệ thống 5C và trên cơ sở đó, tăng năng suất của họ,là một động lực tuyệt vời để áp dụng hệ thống này như một cách sống.
Cải thiện
Bước thứ năm, hoàn thiện hệ thống "5S" trong sản xuất, dựa trên khái niệm kaizen. Nó có nghĩa là tất cả nhân viên, bất kể vị trí của họ, nên cố gắng cải thiện quá trình làm việc trong lĩnh vực được giao phó. Bản chất triết học của kaizen là toàn bộ cuộc sống của chúng ta trở nên tốt hơn mỗi ngày, và vì công việc là một phần của cuộc sống, nên nó cũng không nên xa cách với những cải tiến.
Lĩnh vực hoạt động ở đây rất rộng, vì sự hoàn hảo không có giới hạn. Theo quan niệm của người Nhật, bản thân người lao động nên muốn cải tiến quy trình sản xuất của mình, không cần hướng dẫn hay ép buộc. Hiện nay, nhiều tổ chức đang xây dựng đội ngũ công nhân giám sát chất lượng sản phẩm, truyền dạy kinh nghiệm tích cực của họ cho những người khác và giúp đạt được thành tích xuất sắc.
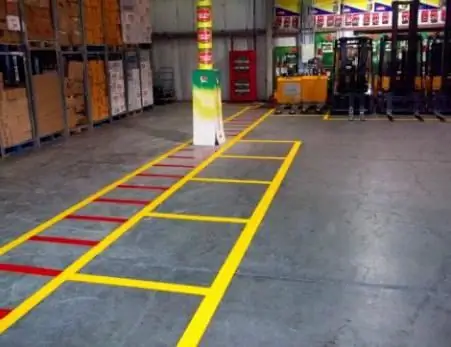
Những lỗi cơ bản
Để hệ thống "5C" bắt đầu hoạt động, việc tổ chức nó hoặc thuê nhân viên là chưa đủ, những người sẽ buộc đồng nghiệp của họ thực hiện nó. Điều quan trọng là mọi người phải nhận ra tính hữu ích của sự đổi mới này và chấp nhận nó như một phong cách sống. Việc đưa hệ thống "5S" vào sản xuất ở Nga đang gặp khó khăn chính vì tâm lý người Nga của chúng tôi khác với người Nhật. Nhiều sản phẩm của chúng tôi có đặc điểm sau:
1. Người lao động, đặc biệt là nếu không có động cơ khuyến khích họ không tìm cách tăng lợi nhuận của doanh nghiệp. Họ đang hỏi,tại sao phải cố gắng làm cho ông chủ giàu hơn nữa nếu ông ấy đã có mọi thứ.
2. Bản thân các nhà lãnh đạo không quan tâm đến việc giới thiệu hệ thống "5S", bởi vì họ không nhìn thấy tính hiệu quả của nó.
3. Nhiều chỉ thị “từ trên cao xuống” đã quen thực hiện chỉ để “đánh dấu”. Ở Nhật Bản, có một thái độ hoàn toàn khác với công việc của họ. Ví dụ, cùng một Taiichi Ohno, khi giới thiệu hệ thống "5S", không nghĩ đến lợi ích cá nhân, mà nghĩ về lợi ích của công ty mà anh ta chỉ là một kỹ sư.
4. Tại nhiều doanh nghiệp, hệ thống 5S đang được áp dụng một cách cưỡng bức. Sản xuất tinh gọn, nghĩa là loại bỏ tất cả các loại tổn thất (thời gian làm việc, nguyên liệu, nhân viên giỏi, động lực và các chỉ số khác), không hoạt động, vì người lao động bắt đầu chống lại những đổi mới ở mức độ tiềm thức, điều này cuối cùng làm giảm tất cả nỗ lực về 0.
5. Các nhà quản lý triển khai hệ thống không hiểu hết bản chất của nó, điều này gây ra thất bại trong các quy trình sản xuất đã thiết lập.
6. Tiêu chuẩn hóa thường phát triển thành bộ máy quan liêu, một hành động tốt bị phát triển quá mức với các chỉ thị và chỉ thị chỉ gây trở ngại cho công việc.
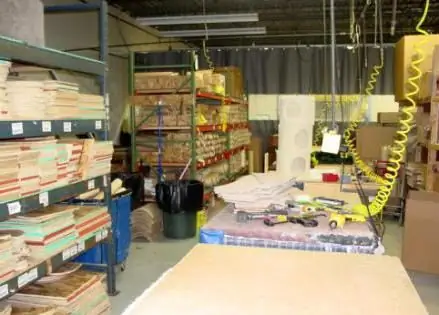
Đánh giá
Người Nga đã đưa hệ thống "5S" vào sản xuất, phản hồi về sự đổi mới này là rất mơ hồ. Ưu điểm nổi bật:
- tốt hơn ở nơi làm việc;
- đừng xao lãng công việc với những việc nhỏ nhặt không cần thiết;
- quy trình làm việc rõ ràng hơn;
- giảm mệt mỏi khi kết thúc ca làm việc;
- tăng nhẹlương nhờ tăng năng suất lao động;
- chấn thương nghề nghiệp giảm.
Khuyết điểm được chú ý:
- khi phân loại, họ buộc phải vứt bỏ mọi thứ;
- tiêu chuẩn hóa đã dẫn đến sự gia tăng bộ máy quan liêu;
- Sự ra đời của hệ thống "5C" không làm trầm trọng thêm các vấn đề trong tất cả các lĩnh vực của doanh nghiệp;
- Việc đặt hệ thống 5S lên vị trí hàng đầu đã làm lu mờ các vấn đề quan trọng như thiếu phụ tùng thay thế.
Đề xuất:
"Hệ thống thông tin phản lực": đánh giá của nhân viên, các tính năng và thông tin thú vị
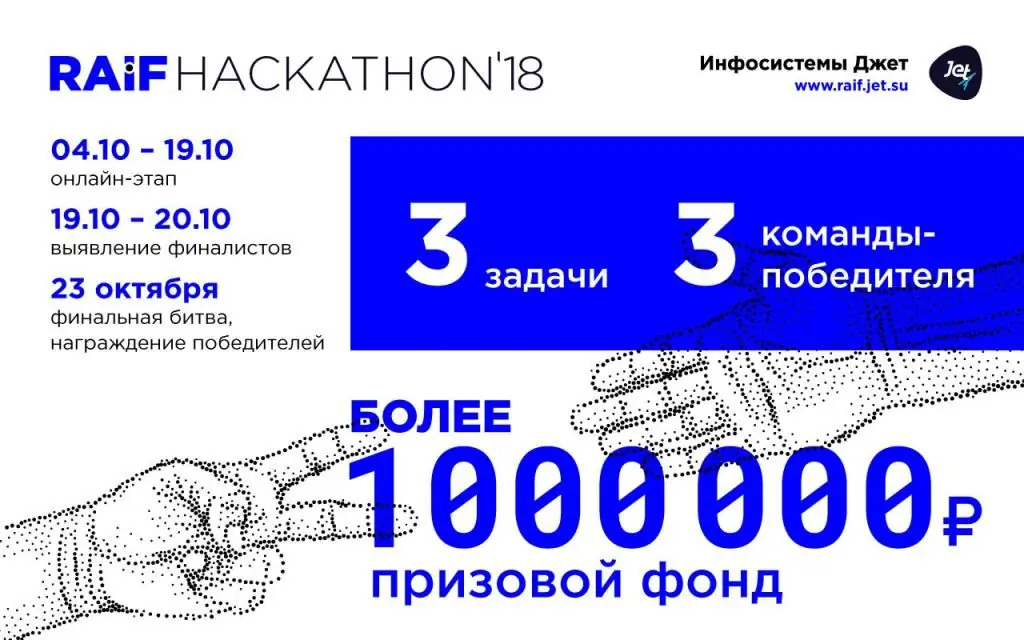
Công nghệ thông tin cho phép bạn tích hợp các giải pháp mới trong sự phát triển của một doanh nghiệp cá nhân hoặc toàn bộ ngành công nghiệp. Nhờ đội ngũ lập trình viên và nhà phát triển, cũng như hoạch định chiến lược, nhiều chỉ số có thể được cải thiện, cũng như có thể tối ưu hóa các chi phí tài nguyên khác nhau. Các giải pháp phần mềm cho bất kỳ ngành công nghiệp nào trong thế giới hiện đại là điều cần thiết. Chúng cho phép bạn nhanh chóng xử lý một lượng lớn dữ liệu và cải thiện quyền truy cập vào chúng
Hợp tác xã sản xuất là Luật Liên bang về hợp tác xã sản xuất. Pháp nhân - hợp tác xã

Kinh doanh không chỉ là một phương tiện làm giàu cá nhân mà còn là một cách để hỗ trợ đáng kể về mặt tài chính cho khu vực đó hoặc tổ chức khác, trong đó phân khúc doanh nghiệp vừa và nhỏ đang phát triển đáng kể. Biết được điều này, hầu hết các cơ quan tự chính phủ đều tích cực ủng hộ (đôi khi thậm chí không phải trên giấy tờ) các sáng kiến của công dân
Phương pháp tổ chức sản xuất: thông số, đặc tính và tiêu chuẩn. Sự cần thiết của phương pháp này trong sản xuất
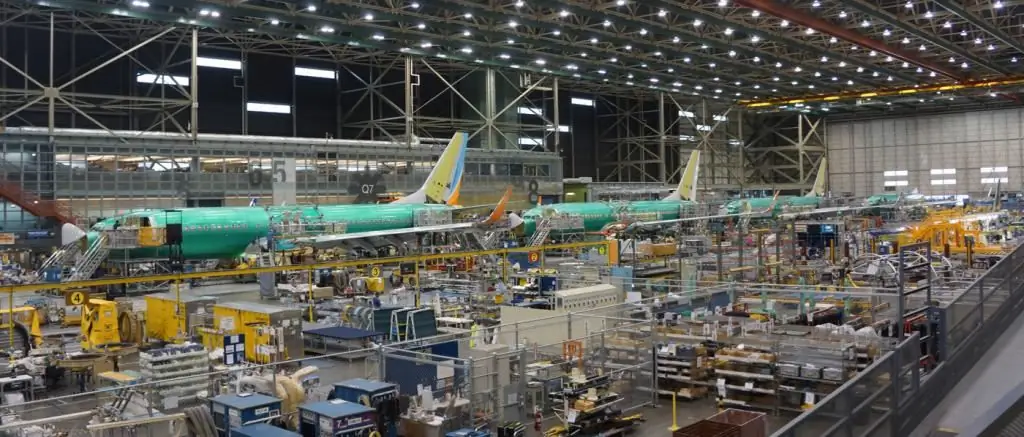
Ngày nay, sản xuất trong dây chuyền là hình thức tổ chức tiến bộ nhất của hệ thống sản xuất. Tốc độ làm việc tối ưu, cường độ lao động tối thiểu và chất lượng sản xuất tối đa - đây không phải là danh sách đầy đủ các ưu điểm của phương pháp đang được xem xét
Nhà sản xuất cáp: loại cáp, danh sách các nhà sản xuất, xếp hạng tốt nhất, chất lượng sản phẩm, địa chỉ và đánh giá của khách hàng
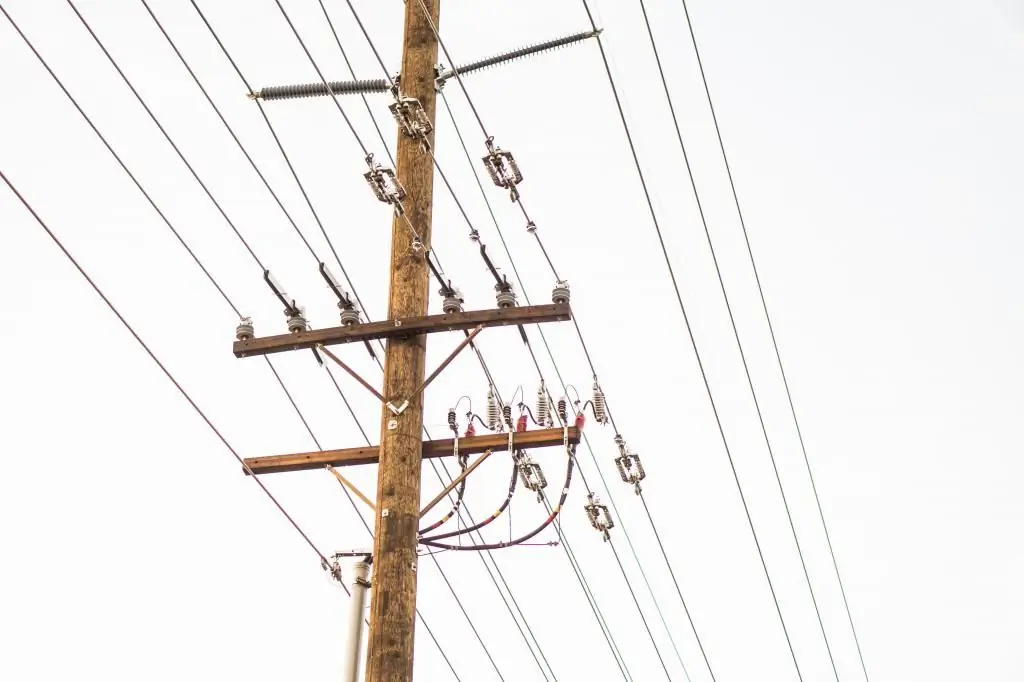
Cáp là một sản phẩm được yêu cầu cao đến mức nó được sản xuất ở bất kỳ trạng thái nào. Dây điện được tìm thấy trong các phòng, mặt đất, các cơ sở công nghiệp và thậm chí cả không khí. Nếu một quốc gia không thể đảm bảo cho mình một sản phẩm tương tự, thì sản phẩm đó là vô giá trị. Bài viết liên quan đến các nhà sản xuất cáp trong nước
Nhà sản xuất vật liệu cách nhiệt: tổng quan về các công ty hàng đầu, sản phẩm được sản xuất, chất lượng, đánh giá
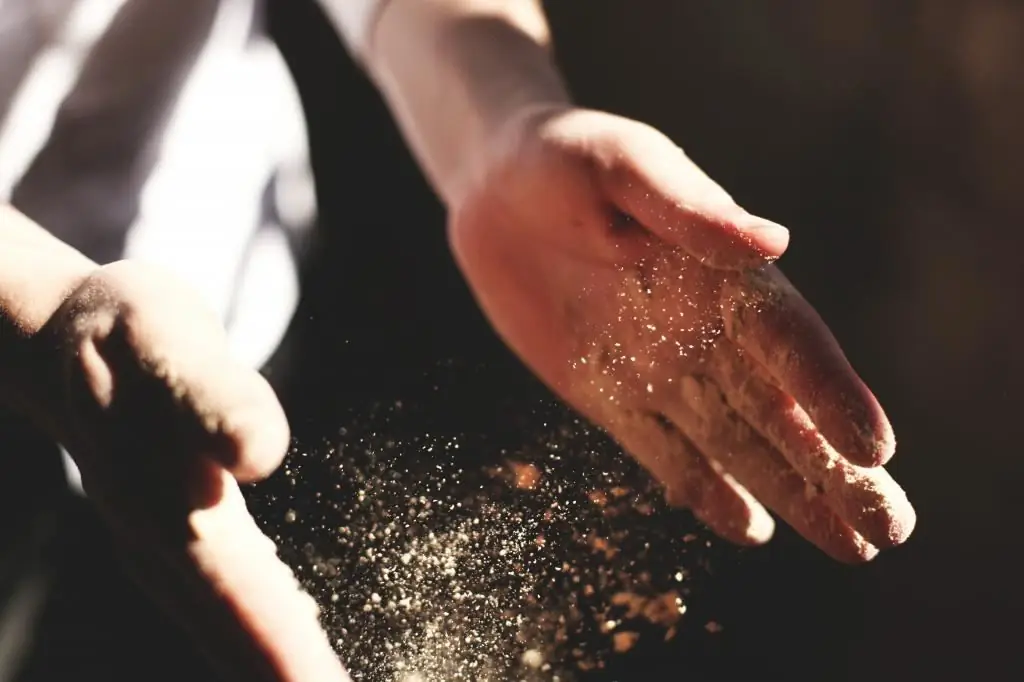
Bông khoáng được sử dụng để cách nhiệt các khe hở trong vách ngăn của tường thạch cao, cũng như trong kết cấu trần. Nó không bắt lửa, đảm bảo bảo vệ bổ sung chống lại hỏa hoạn có thể xảy ra: khi ngọn lửa đến gần bông gòn, nó sẽ tắt. Trong cách điện này, đường kính của các sợi, an toàn môi trường, cũng như các yếu tố kết nối là đặc biệt có giá trị. Bài viết này thảo luận về các nhà sản xuất vật liệu cách nhiệt tốt nhất đáp ứng các tiêu chí trên