2025 Tác giả: Howard Calhoun | [email protected]. Sửa đổi lần cuối: 2025-01-24 13:27
Đúc trong khuôn vỏ còn được gọi là đúc vỏ. Và ở nước ngoài, phương pháp làm việc này được gọi là Shell.
Thông tin chung
Trong ngành công nghiệp ngày nay, người ta sử dụng nhiều phương pháp đúc khác nhau. Ngoài đúc vỏ, đúc đầu tư cũng được sử dụng, cũng như trong khuôn kim loại và một số phương pháp khác. Ưu điểm tổng thể của các phương pháp đúc này, khi so sánh với đúc cát, là chúng tạo ra vật liệu cuối chính xác hơn về hình dạng cũng như kích thước. Ngoài ra, số lượng các vết nhám trên bề mặt của các sản phẩm đó được giảm bớt. Trong một số trường hợp hiếm hoi hơn, nhưng vẫn xảy ra trường hợp loại bỏ nhu cầu gia công tiếp theo sau khi nấu chảy. Ngoài mọi thứ, việc sử dụng đúc trong khuôn vỏ và các phương pháp khác góp phần vào thực tế là quá trình này có thể được cơ giới hóa nhiều nhất có thể, do đó tính tự động hóa của nó cũng tăng lên. Và điều này, tất nhiên, làm tăng đáng kể năng suất của bất kỳ cơ sở công nghiệp nào.
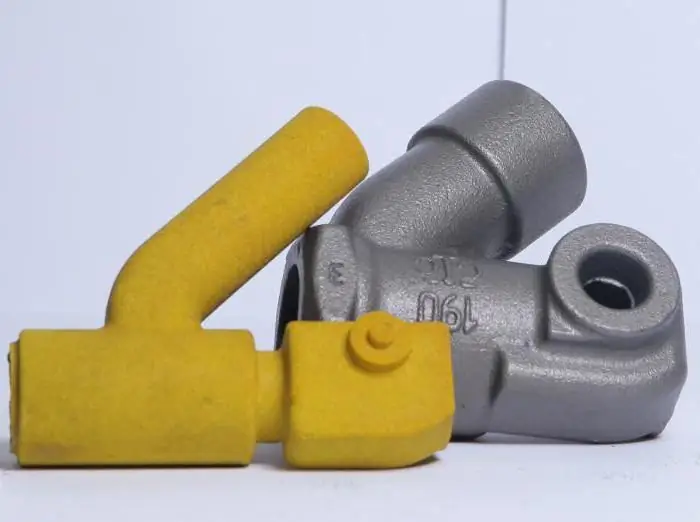
Vỏ đúc
Nếu chúng ta nói cụ thể về điều nàyphương pháp này lần đầu tiên được giới thiệu tại các nhà máy vào năm 1953. Hiện nay, phương pháp được sử dụng khá rộng rãi. Ví dụ, nó được đúc trong khuôn vỏ để sản xuất hầu hết các bộ phận cho máy kéo Kirovets. Tất cả các bộ phận được sản xuất bằng phương pháp này đều có chất lượng cao nhất từ thép hoặc gang. Đúc vỏ là một phương pháp trong đó kết quả cuối cùng của quá trình đúc có hình dạng bao gồm hai vỏ nhựa cát. Ngoài ra, phương pháp chế tạo chi tiết này chỉ được sử dụng trong trường hợp cần chế tạo chi tiết có kích thước vừa hoặc nhỏ nhưng đồng thời có độ chính xác cao. Ví dụ về các ứng dụng cho phương pháp đúc này là các bộ phận động cơ hoặc các vật đúc thành mỏng.
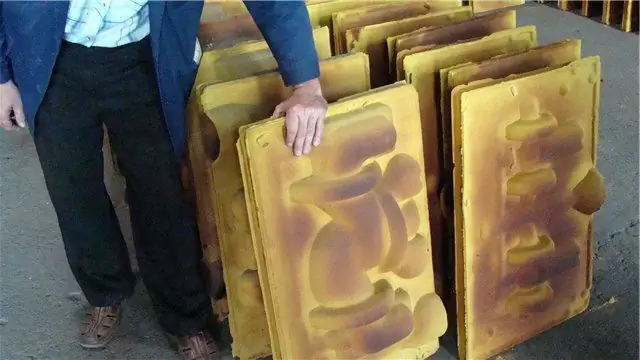
Cốt cách
Với phương pháp làm việc này, bạn có thể nhận được các bộ phận khác nhau cho quạt, động cơ, máy bơm hoặc máy dệt. Tuy nhiên, chiều dài tối đa của sản phẩm nhận được không được vượt quá 1 mét và không được nặng hơn 200 kg.
Bản chất của việc đúc thành khuôn vỏ là dựa trên một số đặc tính nhất định của nhựa nhiệt rắn, là một phần của hỗn hợp cát-nhựa. Ưu điểm của việc sử dụng các thành phần như vậy là các loại nhựa này có xu hướng cứng nhanh chóng và vĩnh viễn khi được xử lý ở nhiệt độ 200-250 độ C.
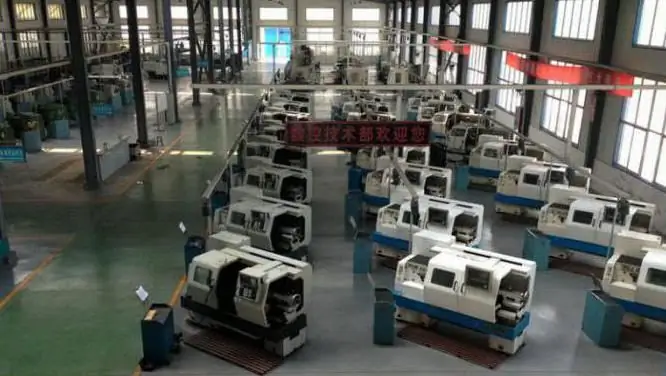
Làm khuôn vỏ để đúc
Để làm khuôn cho quá trình đúc tiếp theo, cần phải có cát thạch anh hạt mịn, đi kèm với việc bổ sung nhựa nhiệt rắn, là yếu tố kết nối của nó để có được khuôn vỏ hoàn chỉnh. Những vật liệu này, đặc biệt là nhựa thông, được chọn vì chúng cứng lại khi vượt qua một rào cản nhiệt độ nhất định. Quy trình sản xuất như sau. Đầu tiên, nhựa được làm nóng đến 140-160 độ C. Dưới tác động của môi trường như vậy, nó biến thành một khối kết dính lỏng bao bọc hoàn toàn khuôn cát thạch anh.
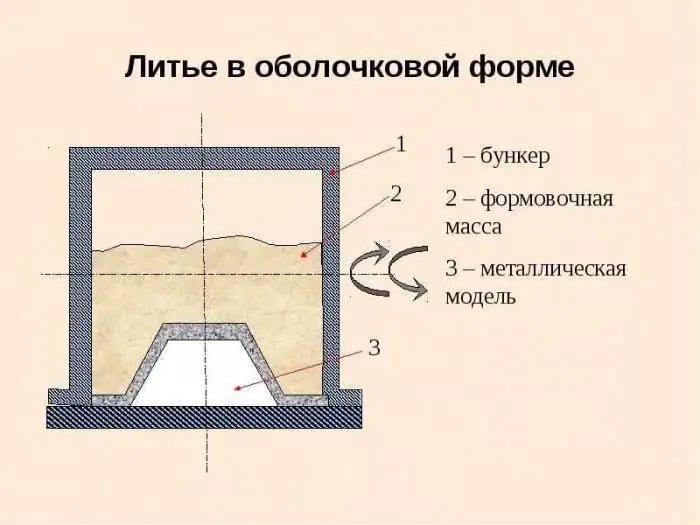
Phạm vi đúc trong khuôn vỏ khá rộng, và do đó quá trình tạo khuôn được chuyển sang chế tạo tự động hoặc tự động.
Sau khi khuôn được phủ hoàn toàn bằng nhựa, nhiệt độ được tăng lên 200-250 độ C. Ngưỡng nhiệt độ này là khá đủ để khối chất kết dính cứng lại và tạo thành hình dạng. Hơn nữa, khi quá trình đúc các bộ phận bắt đầu, tức là khi kim loại nóng chảy đi vào khuôn, nhiệt độ trong đó đạt khoảng 600 độ. Chế độ này đủ để đảm bảo nhựa không bị chảy mà cháy ra ngoài, đồng thời để lại các lỗ rỗng trên khuôn, tạo điều kiện cho khí thoát ra ngoài.
Ưu nhược điểm của đúc khuôn vỏ
Giống như bất kỳ quy trình sản xuất nào khác, quy trình này có những ưu và khuyết điểm. Ví dụ: nếu chúng ta so sánh phương pháp truyền này với truyền trongkhuôn cát thông thường, có một số ưu điểm:
- Sự khác biệt đầu tiên và khá quan trọng là cấp độ chính xác, là 7-9. Ngoài ra, độ hoàn thiện bề mặt của phần thu được được cải thiện lên đến 3-6. Ngoài ra, các khoản phụ cấp được giảm bớt, được phép gia công tiếp theo của chi tiết tạo thành sau khi đúc.
- Một trong những điểm cộng lớn là chi phí nhân công sản xuất vật đúc giảm đáng kể.
- Phương pháp đúc này giúp giảm tiêu thụ vật liệu đúc, cũng như lượng kim loại do kích thước của các rãnh cửa được giảm xuống.
- Giảm đáng kể số lượng đầu ra của hôn nhân.
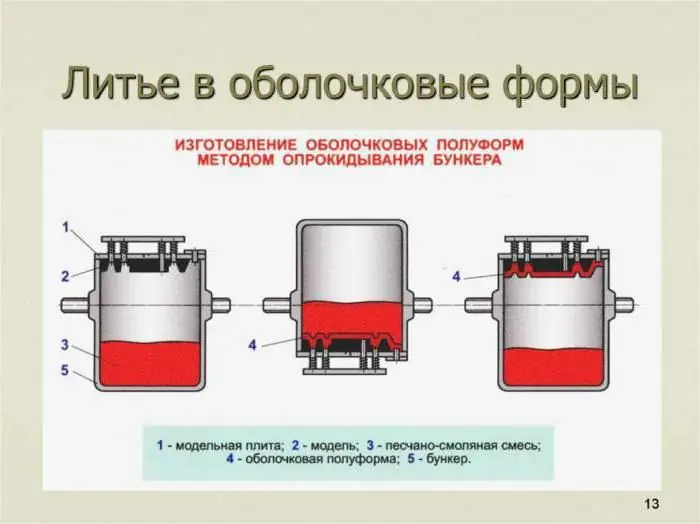
Tuy nhiên, có một số nhược điểm của việc đúc trong khuôn vỏ. Chúng bao gồm:
- Tuổi thọ khuôn vỏ - 1 lần đúc.
- Chi phí cho cát đúc khá cao.
- Phần trăm khí độc hại cao.
Quá trình hình thành cấu trúc
Quá trình hình thành cơ thể được thực hiện trong sáu giai đoạn:
- Bước đầu tiên là quá trình đổ hỗn hợp lên một mô hình kim loại nóng, cũng như quá trình giữ nó trong vài chục giây cho đến khi hình thành một lớp vỏ mỏng và chắc xung quanh bộ phận. Thông thường, các mô hình được làm bằng gang và gia nhiệt của chúng được thực hiện lên đến 230-315 độ.
- Sau đó phải tiến hành thao tác gạt cát đúc thừa. Độ dày của lớp vỏ cuối cùng nên từ 10 đến 20mm. Nó phụ thuộc vào thời gian tồn tại của hỗn hợp trên mô hình, cũng như vào nhiệt độ.
- Sau đó, cần chuyển đĩa mô hình cùng với khuôn vào lò nướng, nơi chúng sẽ ở đó cho đến khi kết thúc quá trình đóng rắn. Khi kết thúc quy trình này, độ bền của vỏ phải từ 2,4 đến 3,1 MPa.
- Sau khi được lấy ra khỏi lò, lớp vỏ cứng được dịch chuyển ra khỏi đĩa. Một bộ đẩy đặc biệt được sử dụng cho quy trình này.
- Sau đó, hai hoặc nhiều mô hình được gắn chặt với nhau bằng một số loại kẹp hoặc bằng cách dán. Những khuôn này có thể được sử dụng để đúc trong khuôn vỏ hoặc lưu trữ đơn giản. Thời hạn sử dụng gần như không giới hạn.
- Trước khi bắt đầu quá trình đúc trong khuôn đã hoàn thiện, người ta sẽ đổ nước bắn vào khuôn, giúp ngăn chặn hoặc phá hủy khuôn trong quá trình đổ tiếp.
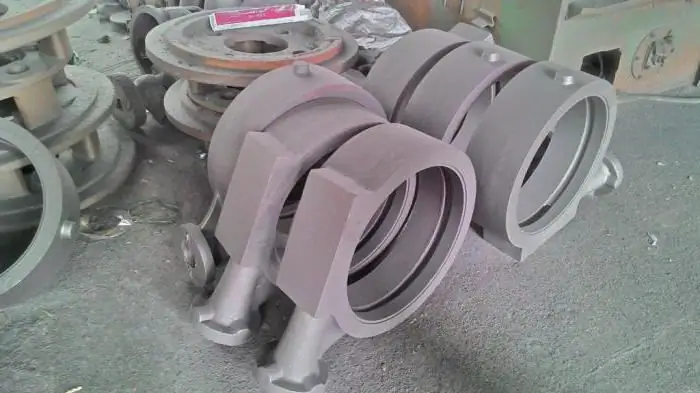
Chi tiết truyền
Điều đáng bắt đầu là dung sai điển hình được phép trong sản xuất dụng cụ có thể là 0,5 mm. Độ nhám bề mặt cho phép trong khoảng từ 0,3 đến 0,4 micron. Các giới hạn như vậy được chứng minh bởi thực tế là cát hạt mịn được sử dụng. Cũng cần lưu ý: việc sử dụng nhựa thông góp phần rất lớn vào việc bề mặt rất mịn.
Số lượng sản xuất
Để tham gia vào quá trình sản xuất khuôn và các bộ phận như vậy, cần phải tham gia vào việc lắp đặt mô hình khuôn. Thời gian cần thiết để cài đặt là ít hơn một tuần. Sau khi cài đặt xong, số lượng đầu ra có thểđạt từ 5 đến 50 cái mỗi giờ. Khối lượng sản xuất mỗi giờ như vậy là khá thực tế, tuy nhiên, để làm được điều này thì cần phải chuẩn bị quá trình đúc cho phù hợp. Các vật liệu chính sẽ được yêu cầu để đúc là gang, nhôm, đồng, cũng như hợp kim của các loại kim loại này. Một vật liệu cần thiết khác sẽ là hợp kim sử dụng nhôm và magiê.
Đề xuất:
Thế chấp ở Đức: lựa chọn bất động sản, điều kiện để được thế chấp, các giấy tờ cần thiết, ký kết thỏa thuận với ngân hàng, tỷ lệ thế chấp, các điều khoản xem xét và quy tắc trả nợ
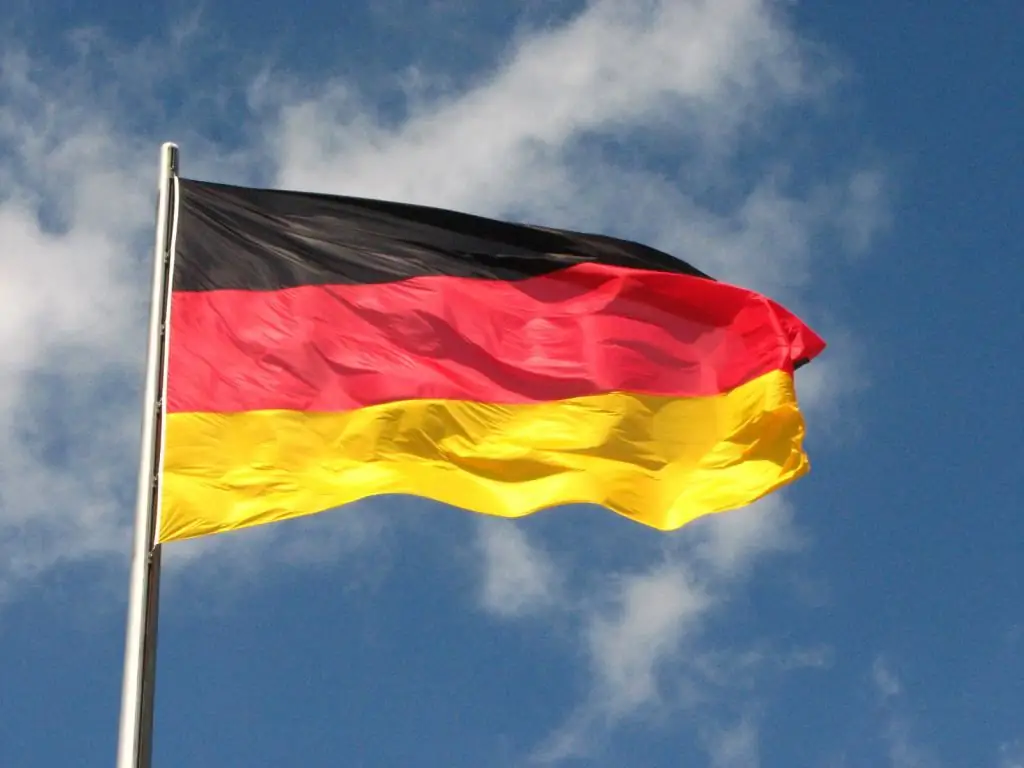
Nhiều người đang nghĩ đến việc mua nhà ở nước ngoài. Ai đó có thể nghĩ rằng điều này là không thực tế, bởi vì giá căn hộ và nhà ở ở nước ngoài quá cao, theo tiêu chuẩn của chúng tôi. Đó là một sự ảo tưởng! Lấy ví dụ, một khoản thế chấp ở Đức. Đất nước này có một trong những quốc gia có lãi suất thấp nhất ở châu Âu. Và vì chủ đề hấp dẫn nên bạn nên xem xét chi tiết hơn, cũng như xem xét chi tiết quá trình vay mua nhà
Kết nối có thể tháo rời: ảnh, bản vẽ, ví dụ, cài đặt. Các loại kết nối có thể tháo rời và kết nối vĩnh viễn

Trong kỹ thuật cơ khí và thiết bị đo đạc, không chỉ các bộ phận được sử dụng trong sản xuất mà các kết nối của chúng cũng đóng một vai trò rất quan trọng. Tưởng chừng như mọi thứ trở nên vô cùng đơn giản, nhưng trên thực tế, nếu bạn đi sâu vào chủ đề này, bạn sẽ thấy rằng có một số lượng lớn các hợp chất khác nhau, mỗi hợp chất đều có những ưu và nhược điểm riêng
Chuyến công tác là gì: khái niệm, định nghĩa, khuôn khổ pháp lý, các quy định về chuyến công tác và quy tắc đăng ký
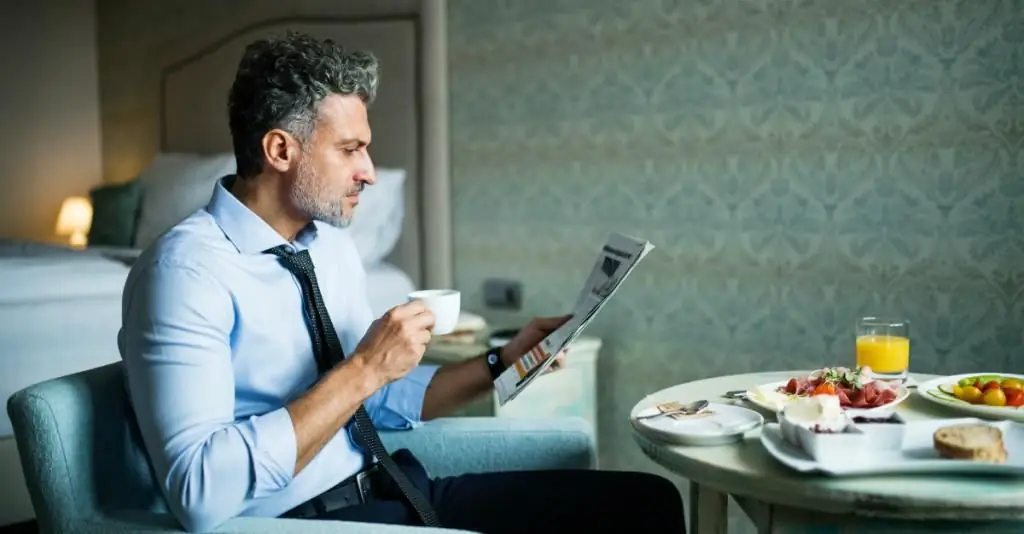
Tất cả người sử dụng lao động và nhân viên nên biết chuyến đi công tác là gì, cũng như cách thức xử lý và trả lương hợp lý. Bài báo mô tả những khoản thanh toán nào được chuyển cho một nhân viên được cử đi công tác, cũng như những giấy tờ do người đứng đầu công ty chuẩn bị
Đúc trong khuôn silicone: thiết bị. Đúc chân không trong khuôn silicone
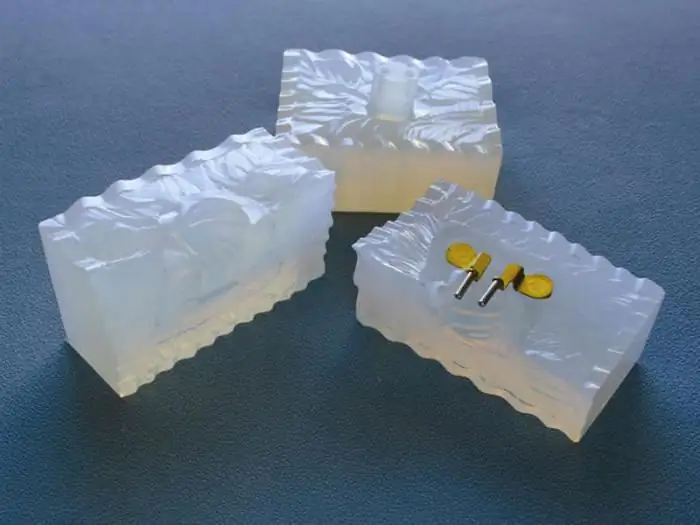
Để sản xuất một số lượng nhỏ phôi nhựa, phương pháp đúc chân không vào khuôn silicone thường được sử dụng nhiều nhất. Phương pháp này khá tiết kiệm (chế tạo một khuôn kim loại đòi hỏi nhiều thời gian và tiền bạc hơn). Ngoài ra, khuôn silicone được sử dụng nhiều lần, và điều này cũng làm giảm đáng kể chi phí sản xuất
Làm thế nào để trở thành một nhân viên bán hàng giỏi: khái niệm về những điều cơ bản của công việc, giai đoạn ban đầu, tích lũy kinh nghiệm, các quy tắc bán hàng, các điều kiện thu
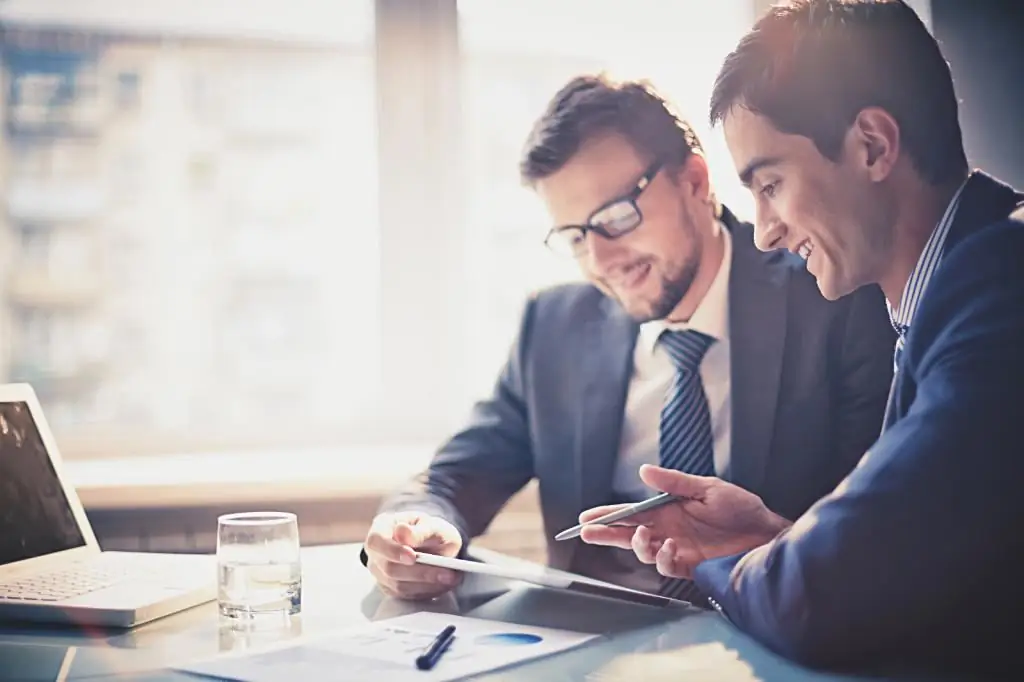
Làm thế nào để trở thành nhân viên kinh doanh giỏi? Bạn cần tài năng, hay một người có thể phát triển một cách độc lập những phẩm chất cần thiết trong bản thân? Bất kỳ ai cũng có thể trở thành một nhà quản lý giỏi. Chỉ là đối với một số người, việc đạt được kỹ năng cần thiết sẽ rất dễ dàng, trong khi những người khác sẽ phải nỗ lực rất nhiều. Nhưng cuối cùng, cả hai đều sẽ bán chạy như nhau